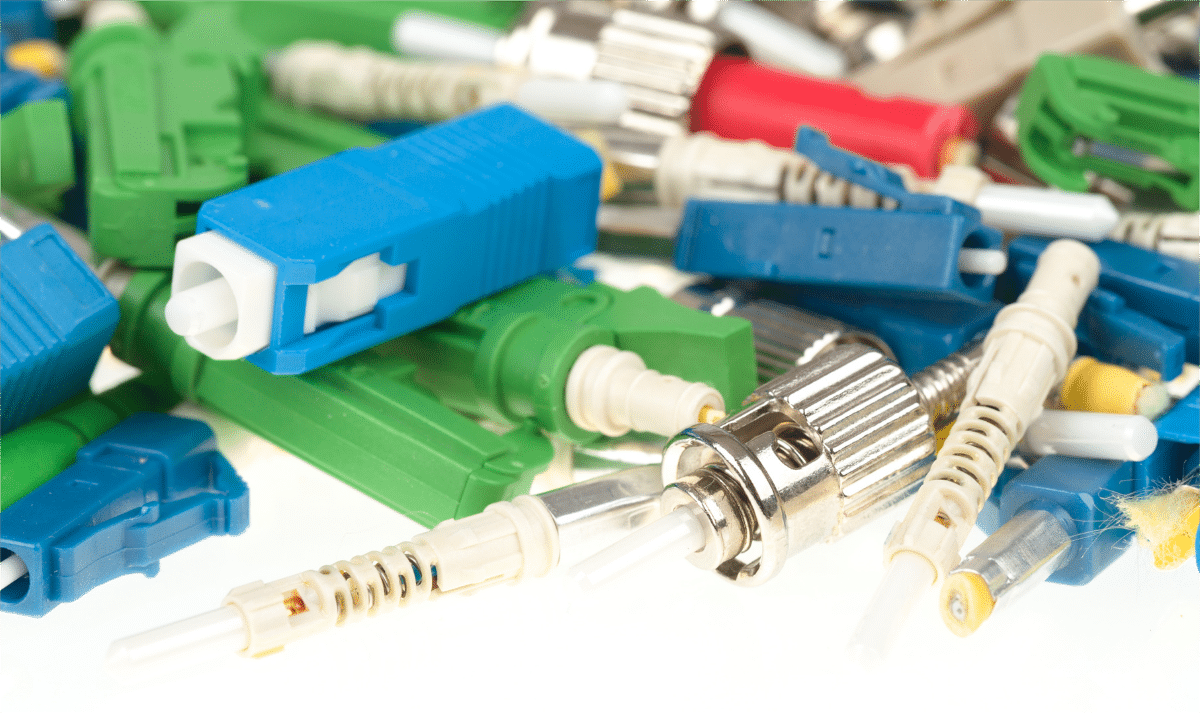
Polishing fiber optic ends is a critical process in ensuring the efficiency and reliability of fiber optic connections. Properly polished ends reduce signal loss and improve the overall performance of the fiber optic network.
This comprehensive guide will walk you through the entire process of fiber optic polishing, from understanding the types of connectors to the detailed steps of the polishing process. Whether you’re a professional technician or a hobbyist, this guide will provide valuable insights into achieving optimal results.
Understanding Fiber Optic Connectors
Fiber optic connectors are essential components in fiber optic networks, allowing for the connection and disconnection of optical fibers. There are several types of connectors, each with its unique characteristics and applications.
Types of Connectors
- SC (Subscriber Connector): Known for its square shape and push-pull mechanism, SC connectors are widely used in data communication and telecommunication networks.
- LC (Lucent Connector): Featuring a smaller form factor, LC connectors are ideal for high-density applications, such as data centers.
- ST (Straight Tip): With a bayonet mount, ST connectors are commonly used in networking environments.
- MTP/MPO (Multi-Fiber Push-On/Pull-Off): These connectors are designed for high-density connections, typically found in data centers and large-scale networking setups.
Significance of Polished Ends
Polished fiber optic ends are crucial for:
- Minimizing Insertion Loss: Ensuring minimal signal loss at the connection point.
- Reducing Return Loss: Preventing signal reflection back into the fiber, which can cause interference and degrade performance.
Equipment Required for Polishing
To achieve a high-quality polish on fiber optic ends, specific equipment and materials are necessary. This section will cover both manual methods and polishing machines.
Polishing Machines vs. Manual Methods
- Polishing Machines: These machines offer consistency and efficiency, especially for high-volume applications. For example, the Domaille 5200 provides precise pressure control and orbital motion, ensuring optimal polishing results.
- Manual Tools: Manual polishing tools provide greater control in low-volume applications. Hand polishing involves using polishing pucks and films on a flat surface, allowing for meticulous attention to detail.
Types of Polishing Films and Their Grit Sizes
Polishing films are graded by their grit size, typically ranging from 1 micron to 12 microns. Each grit size serves a specific purpose in the polishing process:
- 12-10 Microns: Used for initial rough polishing to shape the fiber end.
- 5 Microns: Intermediate polishing to smooth the surface.
- 3-1 Microns: Fine polishing to achieve a smooth finish.
- 0.5-0.3 Microns: Final polishing for optimal performance and minimal signal loss.
Other Necessary Tools and Materials
- Cleavers: Essential for cutting the fiber to a flat surface before polishing.
- Cleaning Wipes: Used to remove debris and contaminants that could interfere with the polishing process.
- Thickness Gauges: Measure the protrusion of the fiber from the ferrule to ensure proper alignment.
- Polishing Pucks: Hold the connector in place during manual polishing.
- Polishing Pads: Provide a flat, hard surface for polishing.
The Process of Polishing Fiber Optic Ends
Polishing fiber optic ends involves several meticulous steps to ensure the end face is perfectly smooth and aligned. This section will detail each step of the process.
Preparing the Fiber: Cleaving and Cleaning
Before polishing, the fiber must be cleaved to create a flat surface. A high-quality cleaver ensures a clean, precise cut. After cleaving, the fiber should be thoroughly cleaned using appropriate cleaning wipes to remove any debris or contaminants.
Step-by-Step Polishing Procedure
- Applying Initial Grit: Start with a rough grit film (12-10 microns) to shape the fiber ends adequately. Use consistent pressure and a figure-eight motion to ensure even polishing.
- Progressing Through Finer Grits: Gradually move to finer grit films (such as 5 and 3 microns) for smooth polishing. Regularly inspect the fiber end using a microscope to check for quality.
- Final Polishing: Use the finest grit films (0.5-0.3 microns) for the final polish. This step ensures the end face is smooth and free of any imperfections.
- Final Inspection: Use a fiber scope to inspect the polished ends. Look for any scratches, pits, or other defects that could affect performance.
Tips for Achieving Optimal Results
- Consistent Pressure: Maintain consistent pressure throughout the polishing process to avoid uneven surfaces.
- Cleanliness: Ensure all surfaces and tools are clean to prevent scratches or debris from affecting the quality of the polish.
- Proper Technique: Use a figure-eight motion during manual polishing to achieve an even polish.
Common Mistakes to Avoid
Polishing fiber optic ends can be challenging, and certain mistakes can compromise the quality of the connection. Here are some common pitfalls to avoid:
Over-polishing and Its Effects
Over-polishing can damage the fiber core, leading to poor performance. It can also create a concave end face, which increases insertion loss and reduces the efficiency of the connection.
Inconsistent Pressure Application
Applying uneven pressure during polishing can result in an uneven surface, affecting the quality of the connection. Consistent pressure ensures a smooth, even polish.
Importance of Cleanliness
Contamination can compromise the effectiveness of the connector. Always clean the polishing films, pucks, and fiber ends thoroughly before and after polishing to prevent any debris from interfering with the process.
Advanced Techniques and Considerations
Advanced techniques and considerations can make a significant difference for those looking to achieve the highest level of precision and performance.
Automated Polishing Systems
Automated polishing systems offer unparalleled consistency and precision. These systems are ideal for high-volume production environments where uniformity is critical. They can be programmed to follow specific polishing protocols, ensuring consistent results every time.
Environmental Factors
Environmental factors, such as temperature and humidity, can affect the polishing process. It’s essential to maintain a controlled environment to achieve the best results. High humidity can cause polishing films to wear out more quickly, while extreme temperatures can affect the adhesive properties of the films.
Quality Control and Testing
Implementing rigorous quality control and testing procedures ensures that polished fiber optic ends meet the required standards. Regularly inspect the polished ends using high-magnification microscopes and conduct insertion loss and return loss tests to verify performance.
Conclusion
Polishing fiber optic connectors is a meticulous process that requires attention to detail, proper equipment, and adherence to best practices. Following the outlined procedures and avoiding common mistakes can achieve professional-grade results that ensure high-performance connections with minimal signal loss.
Whether you’re working with high-volume automated machines or manual methods, the key to success lies in consistent practice and a commitment to quality.
In summary, properly polishing fiber optic ends is essential for anyone working with fiber optics. With careful preparation, adherence to techniques, and investment in quality tools, you can significantly improve connection quality. With practice, polishing skills can enhance dramatically—ensuring the best for your fiber optic installations. For more detailed guides, tools, and resources on fiber optic polishing, be sure to visit AbrasivesHub.com.